What is Porosity in Welding: Ideal Practices for Avoiding Permeable Welds
What is Porosity in Welding: Ideal Practices for Avoiding Permeable Welds
Blog Article
Understanding Porosity in Welding: Discovering Causes, Impacts, and Prevention Strategies
Porosity in welding is a consistent obstacle that can significantly influence the top quality and integrity of welds. As specialists in the welding industry are aware, understanding the causes, impacts, and avoidance techniques associated with porosity is important for accomplishing robust and trusted welds. By diving into the origin of porosity, examining its harmful results on weld high quality, and discovering efficient avoidance techniques, welders can improve their understanding and skills to generate premium welds regularly. The detailed interaction of variables contributing to porosity needs an extensive understanding and a positive method to ensure effective welding end results.
Usual Root Causes Of Porosity
Porosity in welding is largely triggered by a mix of factors such as contamination, incorrect protecting, and poor gas coverage throughout the welding procedure. Contamination, in the kind of dust, oil, or corrosion on the welding surface, develops gas pockets when heated, resulting in porosity in the weld. Incorrect securing occurs when the shielding gas, commonly made use of in processes like MIG and TIG welding, is unable to fully safeguard the molten weld pool from responding with the bordering air, leading to gas entrapment and succeeding porosity. In addition, insufficient gas coverage, usually due to inaccurate circulation rates or nozzle positioning, can leave parts of the weld unsafe, permitting porosity to form. These elements jointly add to the formation of spaces within the weld, damaging its stability and potentially creating architectural concerns. Understanding and attending to these common causes are crucial actions in protecting against porosity and making certain the high quality and toughness of welded joints.
Effects on Weld Top Quality
The existence of porosity in a weld can significantly jeopardize the overall high quality and honesty of the bonded joint. Porosity within a weld produces gaps or dental caries that damage the framework, making it a lot more prone to splitting, deterioration, and mechanical failing.
Additionally, porosity can hinder the effectiveness of non-destructive screening (NDT) strategies, making it testing to find other problems or gaps within the weld. This can lead to significant safety and security worries, particularly in critical applications where the structural honesty of the welded elements is paramount.
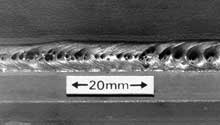
Avoidance Techniques Introduction
Given the destructive influence of porosity on weld quality, effective avoidance strategies are vital to preserving the architectural integrity of bonded joints. Furthermore, selecting the suitable welding parameters, such as voltage, current, and travel speed, can assist decrease the threat of porosity development. By integrating these prevention techniques into welding practices, the occurrence of porosity can be significantly decreased, leading to stronger and extra trustworthy welded joints.
Value of Appropriate Protecting
Correct securing in welding plays a critical duty in preventing atmospheric contamination and making sure the stability Continue of bonded joints. Protecting gases, such as argon, helium, or a mix of both, are commonly utilized to protect the weld pool from responding with components in the air like oxygen and nitrogen. When these responsive elements enter contact with the hot weld swimming pool, they can trigger porosity, bring about weak welds with decreased mechanical properties.
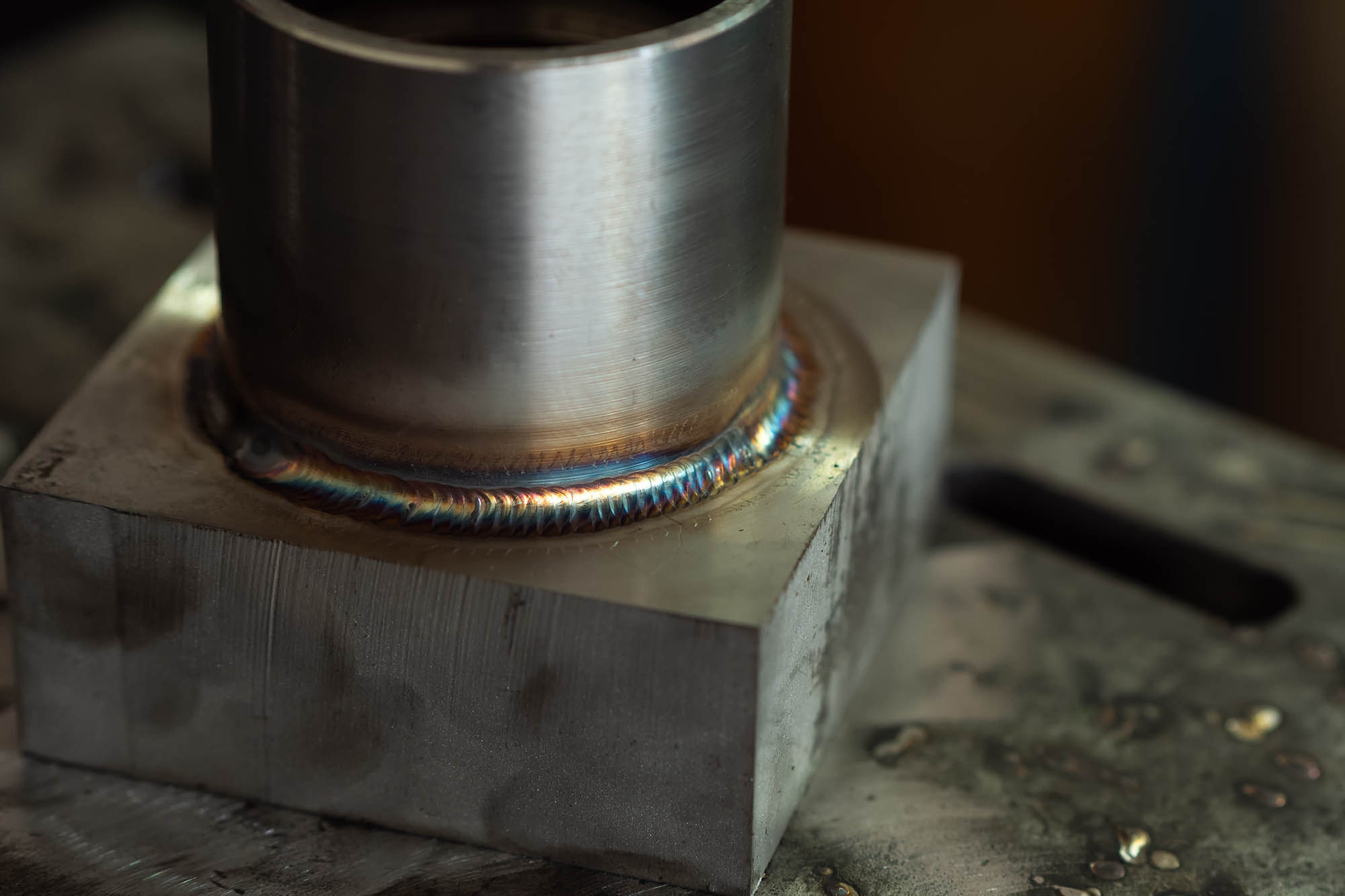
Insufficient securing can result in different problems find more info like porosity, spatter, and oxidation, endangering the structural honesty of the bonded joint. Adhering to correct securing methods is crucial to generate high-quality welds with marginal defects and ensure the durability and dependability of the bonded elements.
Surveillance and Control Approaches
How can welders successfully monitor and manage the welding procedure to guarantee optimal results and stop issues like porosity? By continuously keeping an eye on these variables, welders can recognize discrepancies from the suitable conditions and make prompt changes to avoid porosity development.

In addition, carrying out appropriate training programs for welders is vital for checking and managing the welding process efficiently. What is Porosity. Educating welders on the relevance of keeping consistent specifications, such as appropriate gas protecting and take a trip rate, can assist avoid porosity problems. Regular analyses and accreditations can additionally ensure that welders excel in monitoring and i thought about this regulating welding processes
Additionally, making use of automated welding systems can boost monitoring and control capacities. These systems can specifically manage welding parameters, reducing the likelihood of human error and ensuring constant weld quality. By combining advanced tracking modern technologies, training programs, and automated systems, welders can effectively keep an eye on and control the welding procedure to lessen porosity issues and accomplish high-quality welds.
Verdict
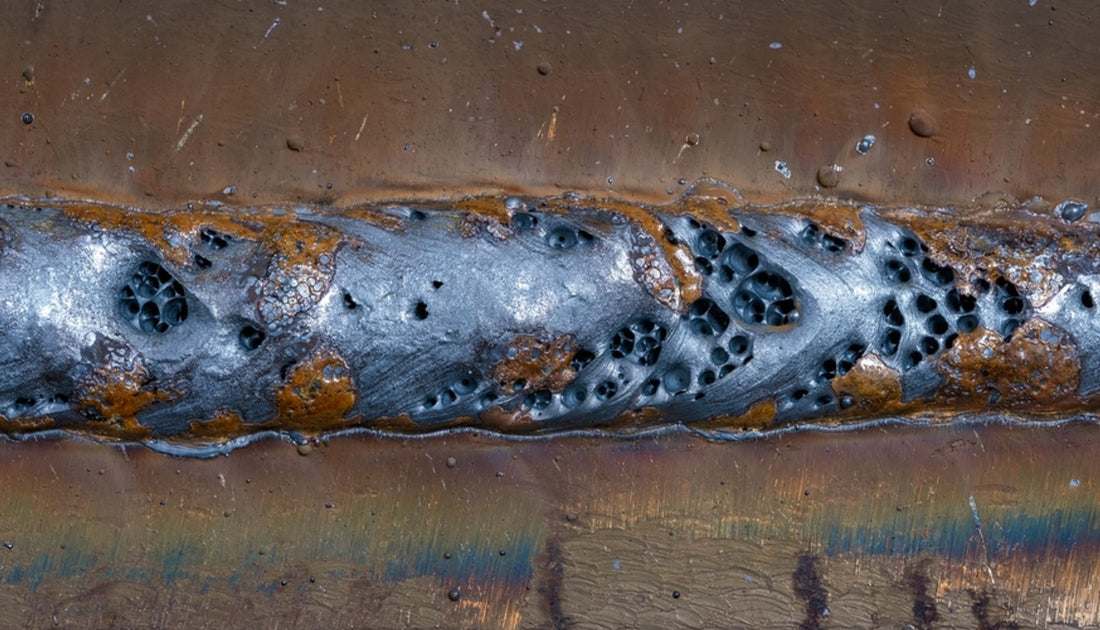
Report this page